The car suspension bible - how car suspension works including shocks, struts, springs, raising and lowering your suspension, different types of suspension, all the technologies involved, DIY car maintenance and much more.
The Suspension Bible
Hydrolastic Suspension
If you've got this far, you'll remember that Dr. Alex Moulton originally wanted the Mini to have Hydrolastic suspension - a system where the front and rear suspension systems were connected together in order to better level the car when driving.
The principle is simple. The front and rear suspension units have Hydrolastic displacers, one per side. These are interconnected by a small bore pipe. Each displacer incorporates a rubber spring (as in the Moulton rubber suspension system), and damping of the system is achieved by rubber valves. So when a front wheel is deflected, fluid is displaced to the corresponding suspension unit. That pressurises the interconnecting pipe which in turn stiffens the rear wheel damping and lowers it. The rubber springs are only slightly brought into play and the car is effectively kept level and freed from any tendency to pitch. That's clever enough, but the fact that it can do this without hindering the full range of motion of either suspension unit is even more clever, because it has the effect of producing a soft ride. Pictures and images of anything to do with hydrolastic suspension are few and far between now, so you'll have to excuse the plagiarism of the following image. The animation below shows the self-leveling effect - notice the body stays level and doesn't pitch.
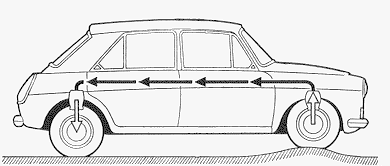
But what happens when the front and rear wheels encounter bumps or dips together? One cannot take precedent over the other, so the fluid suspension stiffens in response to the combined upward motion and, while acting as a damper, transfers the load to the rubber springs instead, giving a controlled, vertical, but level motion to the car.
Remember I said the units were connected with a small bore pipe? The restriction of the fluid flow, imposed by this pipe, rises with the speed of the car. This means a steadier ride at high speed, and a softer more comfortable ride at low speed.
Hydrolastic suspension is hermetically sealed and thus shouldn't require much, if any, attention or maintenance during its normal working life. Bear in mind that hydrolastic suspension was introduced in 1964 (on the prototype BMC ADO16) and you'd be lucky to find a unit today that has had any work done to it.
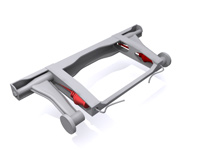
The image here shows a typical lateral installation for hydrolastic rear suspension. The suspension swingarms are attached to the main subframe. The red cylinders are the displacer units containing the fluid and the rubber spring. The pipes leading from the units can be seen and they would connect to the corresponding units at the front of the vehicle.
Hydrolastic suspension shouldn't be confused with Citroën's hydropneumatic suspension (see below). That system uses a hydraulic pump that raises and lowers the car to different heights. Sure it's a superior system but it's also a lot more costly to manufacture and maintain. That's due in part to the fact that they don't use o-rings as seals; the pistons and bores are machined to incredible tolerances (microns), that it makes seals unnecessary. Downside : if something leaks, you need a whole new cylinder assembly.
Hydrolastic was eventually refined into Hydragas suspension.......
Hydragas Suspension
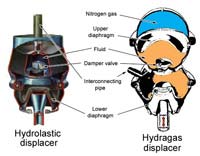
Hydragas is an evolution of Hydrolastic, and essentially, the design and installation of the system is the same. The difference is in the displacer unit itself. In the older systems, fluid was used in the displacer units with a rubber spring cushion built-in. With Hydragas, the rubber spring is removed completely. The fluid still exists but above the fluid there is now a separating membrane or diaphragm, and above that is a cylinder or sphere which is charged with nitrogen gas. The nitrogen section is what has become the spring and damping unit whilst the fluid is still free to run from the front to the rear units and back.
Hydragas suspension was famously used in the 1986 Porsche 959 Rally car that entered the Paris-Dakar Rally, and today you can find it on the MGF Roadster.
There are a lot of resources on Hydragas available at one of the MGF club sites on the internet:
http://www.mgfcar.de/hydragas
Hydropneumatic Suspension
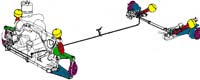
{Thanks to Julian Marsh, Jonathan Bruce, Simon Byrnand and Pieter Melissen for some updates to this information.}
Since the early fifties, Citroën have been running a fundamentally different system to the rest of the auto industry. Its called hydropneumatic suspension, and it is a whole-car solution which can include the brakes and steering as well as the suspension itself. The core technology of hydropneumatic suspension is as you might guess from the name, hydraulics. Ultra-smooth suspension is provided by the fluid's interaction with a pressurised gas, and in this respect, its very similar to the hydragas system described above. Citroën pioneered the system in the rear suspension of the 15 (Traction Avant) model, and it has been fitted to many of their cars since. Because of the complexity of the system, the rest of this section gets a bit wordy but hopefully not so much that I'll lose you half way through. Because this page is about all types of suspension, for clarity I decided to concentrate on the simplified version of this as installed in the "BX" model. If you're desperate to know every last nut and bolt of hydropneumatics, just do a google search for it. On we go....
The system is powered by a large hydraulic pump, typically belt-driven by the engine like an alternator or an air conditioner. the pump provides fluid to an accumulator at pressure, where it is stored ready to be delivered to servo a system. This pump may also be used for the power steering and the brakes, and in the DS for the semi-automatic gearbox. Note - the C5 and C6 only use the high pressure hydraulics for the suspension - brakes and steering are conventional.
Under the company's new Peugot management, Citroën produced the LN, followed by the Visa and then the LNA and then the BX. The BX was a major turning point in Citroën's history. As a direct consequence of the Peugeot influence, the car was somewhat more conventional than its bulkier predecessors like the CX. This Peugeot-enforced "normalisation" of the design makes it fairly easy to examine as an illustration of how hydropneumatic suspension works. The BX employed pseudo-McPherson struts at the front with a hydropneumatic unit replacing the coil spring and damper. At the rear a 'conventional' trailing arm was used with the hydropneumatic unit mounted horizontally.
Apart from the pump, the two most obvious components in the system are the spheres on top of each suspension strut, and the struts themselves. The spheres are like the springs in regular suspension, and the struts are the hydraulic components that make the fluid act like a spring.
The spring in this suspension system is provided by a hydraulic component called a suspension sphere. The accumulator is an additional sphere (which holds a reserve of hydraulic fluid under pressure to even out the load on the pump caused by varying demand) acting rather like a battery. The accumulator is gas (typically nitrogen) under pressure in a bottle contained within a diaphragm. This is effectively a balloon which allows pressurised fluid to compress the gas, and then as pressure drops the gas pushes the fluid back to keep the system's pressure up.
In the image here, the nitrogen gas is represented in red and the LHM fluid is represented in green. As the pressure in the fluid overcomes the gas pressure, the nitrogen is compressed by the diaphragm being pushed back. Then as the pressure in the fluid reduces, the gas pushes back the diaphragm which expels the fluid from the sphere, returning gas and fluid to equilibrium. This is the hydropneumatic equivalent to the spring being compressed and then rebounding.
Still with me? We can keep going...
So how can the interaction of compressing gas, hydraulic fluid and a diaphragm form a spring? Simple(ish): The pressure of the gas is the equivalent to the spring weight. The inlet hole at the bottom of the sphere restricts the flow of the fluid and provides an element of damping. By replacing the spheres for ones of different specifications, it's possible to adjust the ride characteristics of these cars.
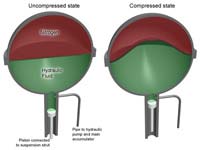
Before we go any further it is pretty important that you understand where the fluid acting on the diaphragm in the sphere gets its force from, and to do that we are going to have to look at the operation of the other key component in the Citroën system - the strut.
The sphere in these systems is actually mounted at the end of the strut. The strut itself acts like a syringe to inject fluid into the sphere. When the wheel hits a bump it rises, pushes the piston back and this squeezes fluid through the tiny hole in the sphere to let the gas spring absorb the energy of the bump. Then when the car is over the bump, the gas pushes the diaphragm back out, pushing the fluid down to the strut, pushing the wheel down to the ground.
Some interesting possibilities were opened up when Citroën decided to use this system to spring their cars. One or two of the more obvious ones are that since the system is hydraulic, the ride height can easily be altered; Citroën put fancy valves called height correctors in the system. They are designed to correct for long-term/static errors in height. To do this there is a clamp on the middle of each roll bar connected by a linkage to the height corrector. This linkage varies by model - on DS, CX, GS, BX it is a simple torsion bar about 8mm diameter and about 400mm long, on the XM and Xantia it is a coil spring assembly with a double acting override linkage, but the functionality is the same. By measuring the height at the middle of the rollbar, it automatically takes the average of the left and right wheel height on that axle, and therefore cannot detect body roll. This prevents it from spuriously trying to react to body roll, as it can't do anything to counter it anyway - it can only make both sides go up or down together.
Additionally the height correctors have a hydraulic damping chamber in them which restricts and delays their movement - typically it takes a suspension movement of at least 20mm in one direction for at least 5 seconds before the height corrector will respond. Even fully bottoming the suspension still takes at least 5 seconds for a response.
This works as a simple averaging system and prevents the height correctors from responding to bumps or road undulations, (which would be undesirable). The slight exception here is the rear suspension which is subject to squat due to acceleration because of the front wheel drive. Prolonged heavy accleration of more than 5 seconds (particularly noticable on an automatic) will cause a height correction response - an undesirable side effect. (Hydractive 2 models take steps to try and avoid this response by stiffening the suspension during heavy acceleration).
Another noteworthy feature of Citroën system is its ability to "pre-set" a car for bumps in the road, keeping the car on an even keel. This is a result of the cross-piping between left and right struts on the same axle. They are connected permanently via a 3.5mm pipe, (except in Hydractive and Activa systems). The height corrector connects to a T-junction of this cross piping, but when the height corrector is "closed" (which is nearly all the time while driving) it represents a dead end, so only the piping from left to right comes into play. When the wheel on one side hits a bump some oil will flow into the sphere on that side via the damping valve, and some will flow across to the other side and extend the wheel on that side, which gives a slight roll stabalizing response. This tends to make the car more steady in the roll axis, and reduces the side to side rocking motion on transverse undulations.
A side effect of this cross piping is that it gives the suspension very soft compliance for "warp mode" movements, as the suspension spheres (springing) don't resist slow roll movements like conventional springs do - only the rollbar does. (This improves traction a lot at very slow speeds over very uneven ground) In fact without the rollbars the suspension would be completely unstable on the roll axis - you could sit on the left and it would go right down and the other side would go right up...
The downside of the cross connection is the same - the long term roll stiffness is provided only by the rollbar - and there is no damping control of the flow of oil from one side to the other, other than some restriction caused by the small pipe diameter - hence the tendency of older Citroëns to have a lot of very slow body roll.
Hydractive 2 overcomes these shortcomings by modifying the side to side connection - it is increased from 3.5mm to 10mm, but at the mid point there is a unit with an additional sphere, an on/off valve, and two damper valves. In the "soft mode" (selected dynamically by computer) this additional middle sphere is connected in circuit and provides additional springing, via the two damping valves in the unit. The system effectively has two parallel paths for the oil to flow for each bump, with different damping rates. The damper valves in the struts spheres on Hydractive 2 are very stiff, while the ones in the middle unit are softer, giving a net result of 3 stage damping in the soft mode, and 2 stage damping in the hard mode. Any body roll requires oil to either flow into and out of the very stiff damping valves in the strut spheres - where the opening thresholds are above that produced by roll movement - or to flow from side to side - where it must pass through two damping valves in series in the centre unit.
This means roll movements are hydraulically damped in Hydractive systems, unlike Hydropneumatic. This contributes towards the reduced roll on later models like XM and Xantia. Because of the large gauge of pipe there is the potential for greater instantaneous flow when hitting large bumps, so the roll axis stability of the car is actually improved over older models.
In the "hard mode", again selected dynamically by the computer based on inputs such as steering wheel angle and road speed, the central unit is isolated, completely blocking the cross-flow of oil and isolating the middle sphere, giving stiffer springing, much stiffer damping, and much reduced body roll.
The Activa refinements and developments were quite effective. The main setback was that ride comfort was even worse than a BMW (although cornering speeds were fantastic) which did not go too well with the traditional Citroën clientele. The current adjustable systems (computer controlled) lack this anti roll characteristic, and there are owners who always prefer the "comfort" setting rather than the "sporty" one, because again, that is not what Citroën is about.

The following cars were fitted with hydropneumatic suspension: Traction Avant 15 Six H, D series, GS/GSA, SM, BX, some XMs and most Xantias. The following were fitted with Hydractive 1 or Hydractive 2 suspension (the difference between H1 and H2 are mainly concerned with computer parameters): most XMs and some Xantias. The Xantia Activa was fitted with Hydractive suspension. The C5 and C6 are fitted with Hydractive 3.
A further mechanical advantage of hydraulic suspension is that the car is able to link its braking effort to the weight on the wheels. In the Citroën BX, the rear braking effort comes from the pressure exerted on the LHM fluid by the weight on those struts. This means that as the weight travels forward under braking, there is less pressure on the back suspension. The suspension then exerts less pressure on its fluid, and as weight and grip diminish on the wheels, so does the braking effort, thus the hydropneumatic system prevents rear wheel lock ups. Since the rear brakes use the rear suspension fluid, the tail is pulled down allowing for level braking.
In addition to these benefits, Citroën pioneered computer controlled suspension in the early nineties by inserting a computer to take readings from the cars' chassis and control systems and let the computer make informed decisions about how to handle the cars suspension. The computer could then effect these decisions by things like servo valves, and offered benefits like soft suspension for cruising, but stiffer, sportier suspension for faster harder driving, allowing the driver to cruise in comfort and still enjoy a responsive car. It also moves substantially towards eliminating body roll and if used for a sportier driver will save tyre wear as well (they claim).
Its worth noting that when Mercedes launched their latest 600 SLC version with a computer controlled anti roll system, Auto Motor und Sport then proudly claimed that to be the first such anti roll system in world, only having to correct that one issue later by having to mention a French invention.
Rolls Royce was the only company ever to buy the patent and they used it in the rear suspension of the Silver Shadow. When Citroën was the owner of Maserati some of their cars were also hydropneumatised.
More in-depth information can be found here:
http://www.citroenet.org.uk/miscellaneous/suspension/suspension8.html
http://www.tramontana.co.hu/citroen/guide/guide.php.
Meanwhile, the rest of us can hopefully feel satisfied with our newly enriched understandings of hydropneumatic suspension. If you're still awake.
Hydraulic Suspension
Hydraulic suspension is an innovation making its way into motor sports, no doubt to trickle down to consumer vehicles eventually. It has been designed by a Spanish company called Creuat and pioneered by the Racing For Holland Dome S101 sports car team. In the image below you can see both the traditional coilover system (the yellow/blue/red units) at the front of the car. This photo was taken before scrutineering for the 2005 24 Hours of Le Mans race. The team had both systems online and when scrutineering passed the car, the coilover units were removed, to race for the first time completely with hydraulic suspension.
Central to their system is a control unit mounted next to the cockpit. They tell me the system can't be compared to the hydropneumatic suspension Citroën uses because this system doesn't use a pump and has less than a litre of hydraulic fluid in the entire system.
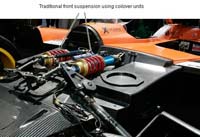
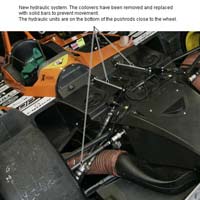
Instead of springs and dampers, this central Hydropneumatic unit takes care of each suspension mode in an independent manner. This allows the car to be tuned to avoid most of the compromises which arise out of the use of conventional suspension made of springs and dampers.
This system is so new that the best source of information on it is Creuat's own website. You can find it at this link and you need to look for the Le Mans Project in their menu on the left side of their page. The hydraulic suspension page is a work-in-progress project and its content changes almost weekly at the moment.
Racecar Engineering magazine have a feature article about this suspension system at this link but you need a subscription to read the whole thing. Fortunately Creuat have scanned the article and made it available as a 6.2Mb PDF file which you can read here.
Thanks to Sander van Dijk for sending me these photos, plus a ton of others of their racing car.
Digital Suspension Systems
Beginning in 2006 with the Audi TT (see below), the concept of fully independent suspension systems came into being. Traditional 'analogue' independent suspension is still connected side-to-side by anti-roll bars. With the advent of computer-controlled suspension systems that are able to rapidly adapt to changing road surfaces, the anti-roll bar is no longer needed. Its function can be replaced as long as sensors and electronically-adjustable suspension can be combined together. For example when the sensors detect body roll in a corner, the suspension components in all four corners of the car can be electronically adjusted to compensate in real-time. Other vehicles that use digital suspension now are the Range Rover Evoque and the Audi R8 but the list will surely grow as it becomes more mainstream.
The next couple of topics deal with two such systems - ferrofluid, and linear electromagnetic suspension.
Ferrofluid or magneto-rheological fluid dampers - Audi Magnetic Ride.
![[ferrofluid]](images/ferrofluid.jpg)
With the 2006 Audi TT, Audi launched their innovative magnetic semi-active suspension. Its a totally new form of damping technology refined from Delphi's MagneRide system. Delphi used to be a division of GM when they developed the first version of Magneride in conjunction with LORD Corp. (The initial version was used in the 2002 Cadillac Seville STS). It is designed once again to attempt to resolve the long-standing conflict between cabin comfort and driving dynamics. The Audi system is a coninuously adaptive system - ie it's a closed feedback loop that can react to changes both in the road surface and the gear-changes (front-to-back weight shift) within milliseconds.
![[2006 audi tt]](images/auditt.jpg)
So how does this work? Well, the dampers in the Audi system are not filled with your regular old shock absorber oil. Nope. They're filled with (wait for it) magneto-rheological fluid. This is a synthetic hydrocarbon oil containing subminiature magnetic particles. When a voltage is applied to a coil inside the damper piston, it creates a magnetic field (physics 101 - get that old textbook out and check the left- and right-handed electro-magnetic rules that make electric motors work). Inside the magnetic field, all the magnetic particles in the oil change alignment in microseconds to lie predominantly across the damper. Because the damper is trying to squeeze oil up and down through the flow channels, having the particles lined up transverse to this motion makes the oil 'stiffer'. Stiffer oil flows less, which stiffens up the suspension. Neat.
You might have seen a demo of a similar system on TV in 2005 when an artist in New York started making living art using a ferromagnetic liquid (ferrofluid) and electromagnets. The principle is exactly the same - apply a magnetic field and the fluid lines up along the lines of magnetism. The image on the left shows a ferrofluid demonstration.
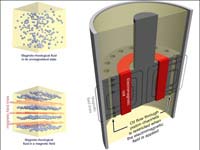
The Audi system has a centralised control unit which sends signals to the coils on each damper. Hooked up to complex force and acceleration sensing gauges, the control unit constantly analyses what's going on with the car and adjusts the damping settings accordingly. Because there are no moving parts - no valves to open or close - the system reacts within microseconds; far quicker than any other active suspension technology on the market today. And because the amount of voltage applied to the coils can be varied nearly infinitely, the dampers have a similarly near-infinite number of settings. The power usage for each strut is around 5 Watts, and the entire thing takes up no more room than a regular coil-over-oil unit. Vorsprung durch Technik indeed.
The diagram here shows the basic principle of magnetised vs. unmagnetised ferrofluid, as well as a cutaway of the piston assembly in a Magneride-type damper. The little blue balls represent the particles of fluid, and yes I know they're huge - that's artistic licence so you can see them.
Linear Electromagnetic Suspension
Picture credits: Bose Suspension Systems & Bose press kit.
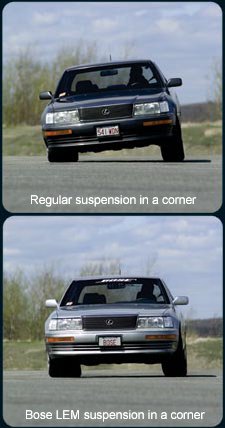
This is another digital suspension systems, invented by Bose®. The idea is that instead of springs and shock absorbers on each corner of the car, a single linear electromagnetic motor and power amplifier can be used instead.
Inside the linear electromagnetic motor are magnets and coils of wire. When electrical power is applied to the coils, the motor retracts and extends, creating motion between the wheel and car body. It's like the electromagnetic effect used to propel some newer rollercoaster cars on launch, or if you're into videogames and sci-fi, it's like a railgun.
One of the big advantages of an electromagnetic approach is speed. The linear electromagnetic motor responds quickly enough to counter the effects of bumps and potholes, thus allowing it to perform the actions previously reserved for shock absorbers.
In it's second mode of operation, the system can be used to counter body roll by stiffening the suspension in corners. As well as these functions, it can also be used to raise and lower ride height dynamically. So you could drop the car down low for motorway cruising, but raise it up for the pot-hole ridden city streets. It's all very clever.
The power amplifier delivers electrical power to the motor in response to signals from the control algorithms. These mathematical algorithms have been developed over 24 years of research. They operate by observing sensor measurements taken from around the car and sending commands to the power amps installed with each linear motor. The goal of the control algorithms is to allow the car to glide smoothly over roads and to eliminate roll and pitch during driving.
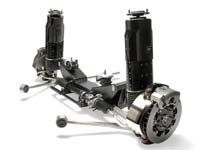
The amplifiers themselves are based on switching amplification technologies pioneered by Dr. Bose at MIT in the early 1960s. The really smart thing about the power amps is that they are regenerative. So for example, when the suspension encounters a pothole, power is used to extend the motor and isolate the vehicle's occupants from the disturbance. On the far side of the pothole, the motor operates as a generator and returns power back through the amplifier. By doing this, the Bose® system requires less than a third of the power of a typical vehicle's air conditioner system. Clever, eh?
Bose have also managed to package this little wonder of technology into a two-point harness - ie it basically needs two bolts to attach it to your vehicle and that's it. It's a pretty compact design, not much bigger than a normal shock absorber.
The official Bose suspension page can be found here if you want more info.
![[aura systems]](images/aurasystems.gif)
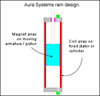
It's worth noting that a company called Aura Systems devised (or at least tried to market) a similar linear electromagnetic suspension system around 1991. They published an article in the Automotive Engineering Journal claiming that electromagnetic actuators could be used for vehicle suspensions and it said that small devices could be designed with a typical thrust capability of about 2500 Newtons and for a reasonable power demand. This happened at the same time that linear electromagnetic rams were being developed for entertainment simulators and full flight simulators to replace hydraulic systems. In fact, it could be argued that the Aura Systems ram was a direct descendant of the rams found on Super-X entertainment simulators.
The units looked very similar to the Bose devices and had the same limitation - they couldn't carry the dead weight of the vehicle. Aura Systems ran into financial troubles in 2000, and filed for Chapter 11 in 2005. The time scales fit quite nicely into the declared Bose time frame (start of development versus going public). Of course they could have been parallel developments, but the bigger question is why was Aura not able to sell their system to an OEM at some time during the previous 15 years? Could it be to do with mechanical limitations - that the sway bars carrying vertical loads are very good at transmitting road inputs into the vehicle structure even if the bar rate is low? Time will tell if Bose manage to succeed where Aura Systems failed.
Air suspension
In days gone by, air suspension was limited to expensive logistics trucks - heavy goods vehicles that needed to be able to maintain a level ride no matter what the road condition. Nowadays, you can retrofit air suspension to just about any vehicle you like from a Range Rover to a Ferrari. Air suspension replaces the springs in your car with either an air bag or an air strut made of high-tensile super flexible polyurethane rubber. Each air bag or strut is connected to a valve to control the amount of air allowed into it. The valves are in turn connected to an air compressor and a small compressed air reservoir. By opening and closing the four valves, the amount of air sent to each unit can be varied. By letting the same amount of air out of all the units, reducing the pressure in the bags, your car gets lowered, whilst increasing the air pressure by the same amount in each unit results in your car lifting higher off the ground. The rubber bags filled with air provide the springing action that used to be the realm of metal springs, and you have the option to maintain the factory (or aftermarket) shock absorbers for - well - absorbing shocks. That's it in a nutshell.
Why air suspension?
Simple : ride quality. A well set up air suspension system can surpass metal spring suspension in just about any situation. If you want a luxurious, smooth, supple ride that will iron out the deepest of ruts and crevasses in the road, air suspension is what you're looking for. It's why logistics firms have used it in their trucks since the year dot - air suspension transmits much less road vibration into the vehicle chassis. There are literally hundreds of combinations and permutations of air bags and struts that can be adapted to fit just about any vehicle and the big hitter in the aftermarket segment at the moment is Air Ride Technologies if you're in America. In England, Rayvern Hydraulics have a similarly complete range of aftermarket solutions. One point to note: for some reason the imperial fittings used on some American systems are all but impossible to get hold of in the UK, so if you're in England and looking for air suspension, Rayvern would be a good choice, or BSS or GAS in Germany.
In factory fit systems, almost any sports sedan that has variable ride height (like a lot of the current crop of Audis) is using air suspension to accomplish this.
Bags and struts
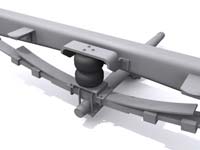
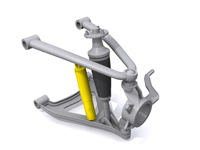
Air bag systems come in two different flavours - air bags and air struts. The bags are typically used for leaf-spring suspension vehicles, but can easily be adapted (through the use of bolt-on brackets) to almost any swinging-arm type suspension system. Air bags are the most reliable systems because of their simplicity. Air struts are a little more complex and come in two flavours - simple struts and pivoting struts. It used to be that you could only have a simple strut because none of the manufacturers had figured out how to keep the air strut sealed when it twisted - a function that is required if you're going to replace a MacPherson strut. Now though, there are a couple of different options for MacPherson strut replacement, the most complex being the twisting double-doughnut style strut that still allows the shock absorber to pass through the middle of it.
The two images here show an air bag system as applied to the rear leaf spring suspension on a truck, and a simple non-twisting air strut system as applied to a double swingarm unit.
Ride height sensors
Simple air suspension is pretty much what I've outlined above, but most systems are far more sophisticated. For example each unit will normally work in conjunction with a ride-height sensor. This is a mechanical lever linked to the suspension arm at one end, and to an electronic resistance pot at the other. The pot is connected to the chassis or frame so that the lever spins the pot as the suspension moves up and down. A computer can use this to read the height of the vehicle in that corner, and with that data, all sorts of wonderful things can happen. For example, if you mash the accelerator pedal, a car will typically squat under acceleration. When this happens, the ride height at the rear of the car gets less. An air suspension system can register this and either send more air to the rear, or reduce the pressure at the front to level off the car again. Same goes for side-to-side roll in corners - air suspension can compensate somewhat for body roll when connected to ride-height sensors. New generation systems also incorporate air pressure sensors to add another level of feedback to the system.
Control panels
In a factory-fit air suspension system, the control panel will either be integrated into the onboard computer (like BMW's i-Drive), or be accessible via a ride-height adjustment control. For aftermarket systems, the control panel is normally a hand-held device with a series of control buttons and LED readouts on it. Either way, the control panel is how you determine what you want the suspension to do, be it hunkered down for sporty driving, or high off the ground for extra clearance.
Low-riders
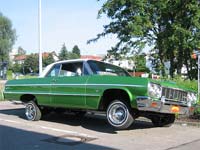
Love 'em or hate 'em, there's no getting around the fact that some petrolheads just love to slam their rides down to the floor but put air suspension systems in capable of making the cars hop, jump and dance. The only real difference with these systems is that they have a much larger high-pressure reservoir normally in the boot or trunk, connected to valves that can open very rapidly. Instead of the smooth, gentle ride-height adjustment of a factory-fit system, these valves can bang open and discharge huge quantities of air from the reservoir into the air bags extremely quickly. The result is the suspension elongating extremely quickly and with enough force to propel the car into the air.
In truth, the extreme low riders like this tend to go more for hydraulic actuators than air suspension. Hydraulics give far more power, far more quickly and are a lot more robust when it comes to the constant hammering they get from competitions and shows. The principle is exactly the same though - a reservoir, a compressor, a set of valves and a set of hydraulic lifters connected to the suspension components. The downside? No suspension to speak of because the hydraulic actuators have no give in them like the rubber air bags do.
Picture credit: Wikipedia / Public Domain