The car brake bible - how brakes work, including disc brakes, drum brake, calipers, hoses, brake fluids and general brake maintenance, current and future brake technologies, DIY car maintenance and much more.
The Brake Bible
Power Brakes and master cylinders.
Power brakes (also known as power assisted brakes) are designed to use the power of the engine and/or battery to enhance braking power. Whilst a fair amount of force can be generated using your foot, using systems from elsewhere in the car to help apply even more force means more powerful brakes as a result.
The four most common types of power brakes are: vacuum suspended; air suspended; hydraulic booster, and electrohydraulic booster. Most cars use vacuum suspended units (vacuum boosters). In this type of system, when the brake pedal is pressed, the push rod to the master cylinder opens a vacuum control valve. This allows vacuum pressure (normally from the intake manifold) to "suck" on a diaphragm inside the vacuum assist unit. This extra vacuum suction helps to produce more force at the pedal end of the brake system.
Hydraulic booster systems usually utilise pressure from the power steering system to augment pressure on the master brake cylinder.
Electrohydraulic booster systems use an electric motor to pressurize the hydraulic system downwind of the brake pedal which has the effect of amplifying the internal pressure in the whole system. The advantage to this system is that as long as there is battery power available, power brakes are available even if the engine fails. With vacuum-assist brakes, no engine means no assistance.
If you're curious about how power brakes work, go out to your car and with the engine off, step on the brakes. They'll have a slightly solid, almost wooden feel to them. Turn the engine on and do it again and you'll notice a lot less back-pressure on the pedal. This is the power assist which is making it easier to depress the pedal.
The components of a master cylinder.
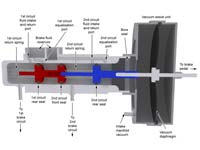
Brake master cylinders are complicated affairs involving finely manufactured parts, minute tolerances, springs, o-rings and rubber seals. The diagram here is a simplified representation of a dual-circuit master brake cylinder. The brake pedal is connected to the main plunger (on the right side of this image). As this is pushed into the master cylinder it acts on the components inside. The rear plunger (in blue) is the first one to start moving. As it moves forward, brake fluid from the reservoir is sucked in through the fluid intake and return port. At the same time, fluid is sucked in through the equalisation port. As the second circuit rear seal passes the intake and return port (about 1.5mm after the plunger starts moving), it creates a fixed volume of fluid between the rear and front plungers. The more the pedal is pressed, the more this fluid is now forced out into the second brake circuit to apply those brakes. At the same time, the pressure building up in this area overcomes the strength of the first circuit return spring and the front plunger (red) begins to move too. As with the rear plunger, it too sucks fluid from the reservoir until the first circuit rear seal passes the fluid intake and return port (again about 1.5mm), trapping fluid between it and the front of the master cylinder. This fluid is then forced out into the first brake circuit, applying those brakes.
When the brake pedal is released, the return springs push the plungers back into their neutral position. Fluid returns to the brake fluid reservoir and the system goes back to an unpressurised state.
One last thing about brake master cylinders: they used to cost an absolute bomb to replace. Historically if a 20-year-old beater developed a leak, it was probably cheaper to buy another used car than to replace the master cylinder. Nowadays not so much. The internet changed all that in the mid to late 90's with online parts stores, which drove prices right down. Now, new master cylinders can be picked for $200 or so. That price break is cheap enough that it becomes silly to get a leaking master cylinder remanufactured instead of just buying a new one.
Cross-linked brakes
(or why there are two brake circuits).
In the rendering of the master brake cylinder above, there are two plungers and two brake circuits. This is the most common design for cars today. It's a form of redundancy in the brake system. The idea is that only two brakes, one front and one rear, are on either of the brake circuits. Therefore, for four brakes, two circuits are needed. But why? Well imagine one of the brake lines springs a leak - for the sake of argument, the front-left brake. If all four brakes were on a single circuit, when the master cylinder began to pressurise the brake system, fluid would spurt out of the broken line and pressure would never build up. In turn, that means none of the brakes would ever come on and you'll sail merrily into the back of the vehicle in front.
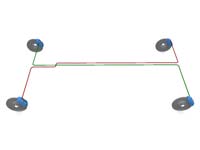
Imagine the same scenario with two circuits. As the first circuit pressurises the front-left and rear-right brakes, fluid spurts out of the broken line and those brakes are never applied. However because the master cylinder is also pressurising a separate second circuit connected to the front-right and rear-left wheels, those brakes do apply and there is still braking force available. Sure, it's reduced, but it's a hell of a lot better than no brakes at all. Because of the front-left to rear-right and front-right to rear-left linking of the brake circuits, this type of system is known as cross-linked brakes. The rendering here shows an example arrangement of cross-linked brakes.
A word about handbrakes.
It's worth spending a moment here to talk about handbrakes. Or parking brakes, e-brakes or emergency brakes depending on where you come from. Whilst they're good for doing handbrake turns, they're not especially effective at actually slowing a car down. They will - don't get me wrong - but they don't exactly have stellar performance so the term 'emergency brake' is a bit of a misnomer. So why is this? Handbrakes are cable-actuated for a start so the amount of power they have is wholly dependent on the amount of tug the driver has in their arm. There's no hydraulic system to help out. Apart from that, they only work on the rear wheels, so it's not as powerful as four-wheel braking. On drum-brakes, the handbrake is connected to a small lever that pivots against the end of one of the brake actuating pistons. When the handbrake is pulled, the lever gets pulled and the brake shoes are pressed out against the inside of the drum.
On disc brakes, the handbrake normally works a second set of brake pads in the rear caliper. They're little spots, about the size of a grown man's thumbprint and they're clamped mechanically against the brake rotor. These pads never need changing because they're normally only used at standstill so generally don't wear much. Their small size is the other reason not to expect stellar stopping performance. That being said, there are derivatives of disc-based handbrakes that use a mechanical arm to press the main brake pads against the rotor although these are less common.
A lot of modern vehicles use electric parking brakes now, and given that the switch to operate them passes a signal through the onboard computer, it has become largely impossible to yank on the parking brake at speed - the car simply won't let it happen. This further amplifies the reason why these are parking brakes and not emergency brakes.
When to use handbrakes
Typically the handbrake ought to used whenever the car is stopped somewhere, be it parked, on a hill or waiting at traffic lights. The reason is simple : when parked or stopped, it's not particularly desirable to have the car run off without the driver. At traffic lights, it's an accident minimisation function as much as anything. If you're sitting there with your foot on the brake and someone drives into the back of you, the impact will cause you to take your foot off the brake and you'll go sailing into the car in front, causing more accidents. With the handbrake applied, in the same scenario, your car will largely stay put (apart from the initial shove across the ground as the energy from the impact is dissapated through the tyres). Of course there are personal habits and mechanical complications to contend with here. For example in a car with an automatic gearbox, it is force of habit to just use the footbrake. Even so, the handbrake should still be used when parked, especially on an incline. The 'park' setting on automatic gearboxes isn't sufficient to hold a car on a hill, and apart from that, it puts incredible strain on the transmission and clutch system by letting the whole weight of the car transfer into the transmission to try to keep it from moving.
In some vehicles, the handbrake isn't a handbrake at all, it's a second footbrake on the far left side of the footwell (or a pull/ratchet handle under the steering wheel). These are basically useless, and are total pain to put on and even more of a pain to get off because it's a one-way ratchet system (the pedal has to be forced all the way down to get it to release). Foot-operated parking brakes also mean it's impossible to do a hill-start in a vehicle with a manual transmission because the foot that would normally be used to balance the clutch, somehow also has to release the parking brake at the same time.
Then there's the ignorance factor. When I went to my new owners orientation evening after buying a Subaru in America, one lady asked what the parking brake was for. (Apparently the name wasn't obvious enough). The dealer representative told her it was a relic of days gone by, not to be used, and he didn't understand why manufacturers even put them in cars any more!
When not to use handbrakes
The first and most obvious answer to this is : when travelling at any speed. If the handbrake is yanked on at any speed much over 30km/h, the back end of the car will start to slide. Great for stunts and tricks, not so great for stopping in 5 lanes of crowded motorway traffic.
The other time to steer well clear of handbrakes is after a decent snowfall, in wet and freezing conditions. With the salt and grit that gets put down on the roads, the salty, snowy slush will be spraying all over the underside of the car. If the handbrake is applied once parked, there is a risk that it will bind on by freezing. Why? Handbrake cables are almost always exposed to the elements at some point under the car. If the cable is covered in slush, as it freezes again it will lock the handbrake on. There's no solution to this other than waiting for the weather to warm up. Well, no solution without becoming a contender for the Darwin Awards, because some people have tried using blowtorches to thaw the ice, not understanding that they were working right underneath the petrol tank. So here's a tip : don't.
If a vehicle needs to be parked in those types of conditions, try to find level ground and leave an automatic gearbox in "p" or a manual gearbox either in first or reverse gears.
Regional variations
One last thing to know about handbrakes : for some reason, from-the-factory settings on handbrakes vary largely with region. In Europe for example, the handbrake is easily capable of exerting enough friction to prevent the engine from being able to move the car from standstill. In America, it's not uncommon to see handbrakes adjusted so lightly that even when fully applied, it's possible to just drive away. The only way to notice is that the handbrake light on the dash is on, there's a subtle lack of performance, and there's a really bad smell of burning as the rear brakes are burning.
Anti lock Braking Systems - ABS
Stop without skidding, and maintain control of the vehicle. That's the premise of ABS. It was first introduced in the 1980's and has been undergoing constant refinement ever since. The system is typically comprised of 4 ABS rings, 4 sensors, an ABS computer and a number of pressure-management circuits in the brake lines. The ABS rings are attached either to the wheels, or more often, to the brake discs. They look like a notched ring - see the image to the right.
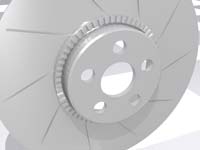
The sensors are magnetic field sensors which are held very close to the ABS rings and can detect the slight change in magnetic field as the teeth on the ring pass them. The pulsing field tells the ABS computer that the wheels are spinning, and how fast they're spinning.
When the brakes are applied, the wheel rotation starts to slow down. The ABS computer "listens" to the input from the sensors and can detect if one wheel is slowing down much quicker than the others - the precursor to the wheel locking up. (This all happens in milliseconds, by the way). When the computer detects this condition, a pressure regulator in the brake circuit interrupts the pressure in the brake lines by momentarily reducing it so that the brakes release just enough to give the wheels a chance to keep spinning rather than locking up. The computer then instructs the regulator to re-apply full pressure and again measures the wheel rotation. This on/off/measure cycle happens around 15 to 30 times a second. If the ABS kicks in, it's normally felt through the brake pedal as a vibration because the pulsing in the brake circuit affects all the components.
Newer generation ABS systems
As technology marches on, so does the control / feedback system used in ABS. It used to be the case that any single wheel approaching lockup would cause the ABS system to pulse the brake pressure for all the wheels. In newer systems, the ABS computer is connected to 4 pressure regulators instead of just the one. This means it can selectively apply pulsed braking only to the wheel(s) that need it. So if three of the tyres are gripping well, but the front-left is beginning to skid, the ABS can unlock the front-left brake and pulse it to try to regain grip. This is called three- or four-circuit ABS and it's all very James Bond. When hooked up to the traction control system, this type of multi-circuit ABS can also be used to influence the overall traction of a car in extreme maneuvers, such as helping to prevent rollover and inside-wheel-lifting by selectively dabbing the brakes only on one wheel.
ABS and skid control
So how to talk about the biggest misconception about ABS - that it will make a car come to a stop more quickly? This is a prickly subject to talk about. In one camp there are drivers like me who just can't stomach the idea of a computer breaking the physical connection between my right foot and the brake system. Whilst in the other camp there are people who believe that ABS is the best thing since sliced bread. It's the people in the second camp who tend to have the all-out belief that ABS will help them stop faster. In certain conditions this is true. On a wet or greasy road surface where the traction is severely reduced, an ABS system can pulse the brakes and prevent lockup much better than a human can. But why is this? The whole point of brakes is to slow the vehicle down. To do that they rely on friction in two places - between the brake pads and the rotors, and between the tyres and road surface. If one of those factors is taken out of the equation, the brakes become useless. The importance of choosing the right rotors and set of brake pads is obvious. The most typical situation is that a driver will panic-react to something and step on the brakes with as much power as they can muster. The brake system amplifies this power, grabs hold of the brake rotors and the wheels stop turning almost instantly. This causes the tyres to now skid across the road surface, and as they do so, they become subject to dynamic attrition. In other words, if a tyre is rotating and gripping the road, the "stick" factor is much higher than if the wheel is locked and skating across the same surface. So that's what ABS does - in an emergency, it ensures that the wheels don't lock up but instead keep spinning so that the tyres maintain grip with the road. (That's where ABS gets its name - Anti-Lock Brakes.) This is where the real benefit of ABS comes into play. When trying to avoid an accident, the best thing to do is to try to steer around it. If the tyres are skidding on the road surface, the direction the front wheels are pointed is largely irrelevant, because at that point the actual direction of travel has everything to do with the direction the vehicle was travelling, combined with the camber of the road. Once the tyres lose grip, all bets are off. With ABS, if those wheels keep turning and the tyres keep gripping, then when the driver ham-fistedly grabs the steering and yanks it to one side, the car will still turn and it might be possible to avoid the accident. So that's the true essence of ABS - to maintain control over the direction of the car.
So why the negativity?
My bone of contention with ABS is not so much to do with the technology as the placebo effect is has on drivers. ABS is widely misunderstood and when asked, most drivers will say that ABS helps them to stop more quickly, and as illustrated above, in certain conditions this is true. But even the most well-trained driver is going to be subject to panic in an emergency, and more often than not, will lock their arms on the steering wheel bracing for the coming impact. When this happens, steering goes out the window so the ABS is trying to allow control but the driver isn't taking advantage of it. Given that this is the most natural human instinct, people accept this as "the way of crashes" but somehow believe that if they have ABS, they'll be able to stop before they get to the point of impact, and that's simply not true. Its true to say that too many people think ABS gives them a license to drive faster, because they mistakenly believe that it will get them out of any situation. It's yet another technical placebo that has been put into vehicles which is making the standard of driving worse. The more gadgets and "driver aids" that get put into a car, the worse the drivers become because they live in a rose-spectacled world where they believe that it's the car's responsibility to get them out of any sticky situation that might arise.
Political correctness and the push for ABS in every vehicle
It's a widely perpetrated myth that speeding is the cause of most accidents, so it follows that if a method can be developed to help drivers to bring their vehicles to a stop in a more controlled fashion, there will be a corresponding reduction in the number of accidents. Good idea, but it doesn't have a lot of substance to it. Check the page with studies on the facts vs. the fiction of speeding, and it becomes obvious that only 4% of all accidents are caused by loss of control of the vehicle with excessive speed as the primary contributing factor. So ABS wasn't really designed for that - it's difficult to reduce the incidence of the already lowest cause of motoring-related accidents. In truth, distracted drivers (as mentioned above, driving in their cosetted mobile living rooms), their actual ability to drive properly (training and advanced driver courses) and their ability to have some form of spatial awareness are much bigger factors than speed, and none of those can be overcome by clever braking systems. Shouldn't we be pushing for more driver training programs to attempt to treat the real cause of the accidents rather than simply putting a bandage on the result?
So what about the emotive issue of pedestrian accidents? What if a driver could stop quicker? It's a staggering fact that 84% of vehicle-pedestrian accidents are actually the pedestrian's fault and in most of those cases, even if the driver could have stopped on a dime, the accident would not have been prevented. Seriously. Read the the facts vs. the fiction of speeding page - you'll be astonished. I'm not condoning running over pedestrians - that would be stupid. I know first-hand what it's like - I had one of those 84% jog out in front of me using his cellphone when I was riding my motorcycle some years ago. I hit him square in the back despite being hard on the brakes, and threw him a good 10 metres down the road. He survived with some scrapes and bruises but I still think about it to this day. I can't begin to imagine what it would have been like if the stupid bugger had actually died.
ABS in snow and ice, and on gravel
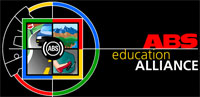
Ah yes. The two camps for this argument are split almost exactly 50/50. In one camp, those like me who from experience would rather have their tyres lock up in deep snow to give me at least a fleeting chance of having them dig through the snow to find some road; who have anecdotal evidence that ABS is total crap in snow and ice. Whilst in the other camp, those who again believe ABS will somehow magically stop them from crashing in the same conditions; who have similar anecdotal evidence disproving all those in the first camp.
ABS by its very nature is designed to stop the wheels from skidding by allowing them to keep turning. On deep packed snow and ice, that's exactly what they're going to do - skid, so ABS effectively removes a considerable amount of braking in an emergency in these conditions. It's why some cars have ABS disable systems for snow and ice, and it's why ice racers yank the fuse to the ABS system before they even get in a car to race.
The ABS Education Alliance, a group aimed to help educate drivers on how ABS will best benefit them, has this to say on the subject:
Even in fresh snow conditions, you gain the advantages of better steerability and stability with four-wheel ABS than with a conventional system that could result in locked wheels. In exchange for an increased stopping distance, the vehicle will remain stable and maintain full steering since the wheels won't be locked. The gain in stability makes the increase in stopping distances an acceptable compromise for most drivers.
So the short answer to this debate is that ABS is worse in snow and ice for overall stopping distance, but better for controlability.
The hidden gremlin of ABS - what is not advertised.
Looking at the statistics for crashes, a large percentage of them are "fender benders" - low-speed impacts that only do a little damage and so slow that the vehicle occupants are in no danger; normally about 10mph. Guess what the typical "minimum activation speed" is for ABS. That's right. On a lot of vehicles, the ABS is useless much below about 10mph. Seriously. Try it. Find an empty road on a slight downhill grade - even better if its on a dewy morning. Run an ABS-equipped car up to about 10mph and jam on the brakes as hard as possible. The car will skid to a stop and the ABS system will remain totally silent.
A final thought on ABS
Consider this: in an accident where the ABS works perfectly, there will be no skidmarks on the road surface. An inspection of the car will show the brakes and ABS system are working perfectly but the absence of skidmarks could lead the police accident scene investigator to believe the driver didn't brake at all. That in turn could lead to that driver being the one "at fault" with all the consequences that involves. Think about it.
Remember : ABS attempts to ensure the car stops in the shortest distance possible for most road surfaces. It is not a substitute for the driver paying attention to the road and their driving.
Brake-assist and collision warning systems
Picture credit: Volvo
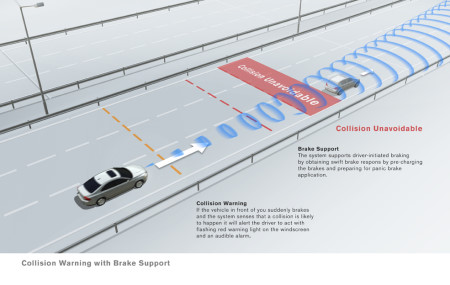
By 2006, brake-assist and accident warning systems were starting to find their way into consumer cars. The side effect is that manufacturers are reinforcing the misconception that the driver is no longer responsible for their actions. Volvo's collision warning system (CWS), for example, constantly monitors speed and uses a radar with a 15° forward field of view to determine the distance to any object in front. If the distance begins to shrink but the driver doesn't slow down, the system sounds a buzzer and flashes a bright red light in a heads-up display. The brake pads are automatically placed against the discs and when the driver finally does use the brakes, the system monitors the pedal pressure. If the pressure is determined to be too light, the braking power is amplified by the system.
It's a great idea, but the TV commercials for this system need some serious attention. Volvo's commercials actually show a woman driving a Volvo, arranging papers on her passenger seat and talking on a cellphone. When the collision warning system activates and she looks up, bemused, then applies the brakes to avoid running into a truck in front of her - a truck that she would have seen and presumably slowed down for had she been paying attention. Whilst it likely wasn't meant to be taken this way, that Volvo commercial actually appears to be promoting distracted driving - Volvo will attempt to save you from your own stupidity because it's just too inconvenient now to be paying attention to the road ahead.
Rather than train drivers to understand that they need to be responsible for their actions, that they need to be alert to their surroundings and that they need to pay attention when they're driving, collision warning systems again attempt to treat the symptoms rather than trying to cure the problem itself.
Brake-assist and auto-brakes go one step further. In some high end vehicle (top end BMWs and Mercedes' for example), the collision-detection system is linked into the brakes as it is with the Volvo system, but it's also been given the flexibility to do all the braking. Adaptive cruise control, for example, will control the throttle just like a normal cruise control system, but will also apply the brakes if it determines that the car is getting too close to the vehicle in front. Full auto-brakes will actually stop the car if the driver fails to respond. All these systems work in essentially the same way - they monitor the brake use and distance to the vehicle in front. If the computer thinks the driver isn't braking hard enough, it will assist.
These systems are all very clever but they tread the thin ethical line. Just because engineers can make their vehicles do this doesn't mean they should. Consider this: with in-vehicle monitoring and tracking systems like OnStar, and the impending satellite-tracking systems for road tolling, it's not too hard to imagine all those systems chained together in such a way that the vehicle will literally prevent a driver from speeding by limiting the throttle availability and controlling the brakes. If you really want to be driven like that, in a vehicle over which you have no control at all, take the bus.
Please don't misunderstand - I think a lot of what Volvo do in vehicle safety is a good idea - the transparent A-pillars, the blind-spot assist and things like that - they all go towards eliminating problems inherent with the design of cars. But I believe putting systems into a car that attempt to compensate for the ineptitude of the person behind the wheel is a mistake. But that's just my opinion.
Like the site? The page you're reading is free, but if you like what you see and feel you've learned something, a small donation to help pay down my car loan would be appreciated. Thank you.
Other Brake Technologies
There are other brake technologies that are becoming available in vehicles now, and a lot of them are gathered together in the many high-end BMW models. They're the rolling embodiment of clever brake engineers just showing off. Three of the more notable features are:
- Brake Drying. The X3 has rain-sensing windscreen wipers. When they sense rain, they also send information to the onboard computer. In turn, it goes into a cycle of occasionally bringing the pads into light contact with the brake rotors. This generates enough friction to eliminate any film of water that might be on the surface of the rotors, but not enough that it slows the car down or is even detectable by the driver.
- Brake Stand-by. This is a pre-emptive system that attempts to detect when sharp braking is about to happen. Potentiometers attached the accelerator can detect when the driver takes their foot off it very quickly. That would normally be followed by the brake being applied very quickly. When the onboard computer senses this condition, it moves the brake pads right up to the rotors using the same mechanism that the brake drying system uses. Ultimately, if the driver does jump on the brakes, they're ready to work the millisecond the driver's foot touches the pedal. It may not sound much but that tiny difference in distance moved, translates into a saving in time between putting a foot on the brake and the car actually slowing down. That in turn translates into forward distance - or less of it.
- Brake Fade Compensation. Right up at the top of the page I explained what brake fade was. If the brake rotor temperature begins to rise, this system increases the hydraulic pressure used to press the pads against the rotors without requiring any more pressure on the brake pedal. I'm not sure if this system has a warning light or not, but it should otherwise drivers could end up driving on horribly faded brakes without realising it, and eventually, even the extra hydraulic pressure isn't going to help.
Unlike the brake-assist and collision-detection systems outlined earlier, these three brake technologies don't actually attempt to compensate for any wrongdoing on the driver's behalf. They simply help prepare the car for when the driver chooses to use the brakes.
Brake hoses - not just rubber.
Obviously with all the pressure in a brake system, the last thing we need is for the brake lines themselves to deform and flex. If they do, brake pressure can be reduced or lost. Rigid steel brake lines are no problem, but for the flexible areas of the brake lines, hoses are required. Brake hoses come in two basic flavours.
Rubber hoses.
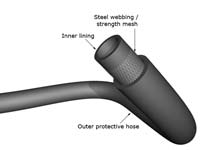
Ah the humble rubber hose. But when used in brake lines, not so humble. Not to be recommended, but if you were to get under your car and cut one of your rubber hoses, you'd notice a couple of things. First, it's amazing how quick all the brake fluid that spills out will stain your clothes and literally eat the paint off your car right in front of you. But second, and more importantly, the hose itself is actually made of three parts. The inner liner is a corrosion and brake-fluid resistant compound designed (normally PTFE / Teflon® based) purely to keep the brake fluid in. Around the outside of that, there's a steel webbed mesh. This is what gives the brake hose its strength and stops it from bulging and deforming. And around the outside of that there's a slightly thicker rubber coating, which is there to weatherproof the steel mesh. The three layers together give strength, flexibility and durability.
Steel-braided hoses.
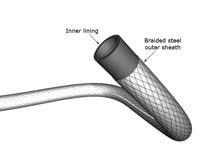
Steel-braided hoses are a slightly different design. They only really have two components - the inner hose which carries the brake fluid and is lined with a PTFE compound, and the outer steel braid which contains and flexing or bulging. Steel-braided lines resist bulging a lot better which is why a lot of aftermarket tuners opt to put them on their vehicles. One downside is that the steel braiding itself is totally merciless and if it finds something to rub against in the vehicle, it will rub right through it, even if it's an alloy. For that reason, a lot of braided brake hose manufacturers put a third layer - a thin transparent rubber sheath around the outside simply to keep everything in check and prevent scuffing and rubbing.
Brake fluids.
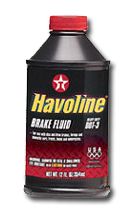
As mentioned elsewhere on the page, brake fluid does not compress. It's a good job too - putting a foot on the brake pedal and having it travel all the way to the floor is less than optimal. But that's exactly what can happen if the "health" of brake fluid is ignored.
Brake fluid is hygroscopic - that means it attracts and soaks up water. This is why it comes in sealed containers, and why when the crazy guy four doors down offers some of the 15 gallons of brake fluid he's had in his garage since the war, it would be wise to turn him down. The problem with it being hygroscopic is that if it does start to take on water, Bad Things can happen. Pull up a chair and let's go through this.
Typical DOT 4 brake fluid (see later for DOT ratings) boils at about 446°F (230°C). Water boils at 212°F (100°C). Imagine brakes that are getting hot because of a long downhill stretch. Whilst the brake fluid is quite OK, the temperature of the brake components might get up over the boiling point of water. If that happens, the water boils out of the brake fluid and forms steam - a compressible gas. Next time pressure is applied to the brake pedal, rather than braking, all the pressure in the brake system is taken up with compressing the steam. Brakes don't work, car doesn't stop.
Getting a little more complex, the boiling point of a liquid goes up with its pressure (Physics 101). So when the brake pedal adds pressure to the brake system, the boiling point of the fluid might actually go up to 500°F (260°C) and the boiling point of the water content might raise up to 250°F (121°C). This is great, right? Now the boiling point is higher than the temperature of the brake fluid. At least it is until the brake pedal is released. At this point the pressure in the system returns to normal, the boiling points revert to normal and instantly the water boils off into steam again. The symptoms are slightly different now. Under this scenario, the brakes work the first one or two times, but on the third or fourth press, they stop working because now the temperature and pressures have conspired to boil the water.
The worst possible scenario is brake-fade combined with air in the system. If this has happened to you, then there's a pretty high probability that you're reading this page from beyond the grave; in most accidents where weak brakes become no brakes, there aren't many survivors.
D.O.T ratings
All brake fluids are DOT rated. The owners handbook for any car or motorbike will probably indicate to use DOT3 or DOT4 from a sealed container. The DOT ratings are a set of minimum standards the fluid must adhere to in order to get the rating, and thus work in a braking system. The following table shows the various properties of DOT ratings. Remember that the values here are the minimum values. Most manufacturers make sure their product far exceeds minimum ratings.
Boiling Point | DOT 3 | DOT 4 | DOT 5 (silicone-based) | DOT 5.1 (non-silicone based) |
---|---|---|---|---|
Dry | 401°F | 446°F | 500°F | 500°F |
Wet | 284°F | 311°F | 365°F | 365°F |
The "dry" and "wet" boiling points in the table above are for brake fluid which is fresh from the bottle (dry) and which has a 10% water content (wet). A DOT study in 2000 discovered that on average, the brake fluid in a vehicle absorbs about 2% water every 12 months.
The two types of brake fluids shown in the table are DOT3/DOT4/DOT5.1 which are glycol (Polyalkylene Glycol Ether) based, and DOT5 which is silicone based. DOT3 and DOT4 fluids are interchangeable* - the only real difference is their boiling point. Theoretically DOT4 and DOT5.1 fluids can be interchanged too but I wouldn't recommend it. DOT3/4/5.1 and DOT5 fluids cannot be mixed or interchanged under any circumstances. They mix like oil and water (ie. they don't) and the silicon based fluids can destroy the seals in brake systems which rely on the moisturiser additives that are present in DOT3/4/5.1 fluids.
Other things to know about silicone based fluids:
- they are resistant to absorbing water, which is why their wet boiling points are so high. Problem is that any water content eventually pools in the low spots of the brake system and causes rust.
- they don't strip paint.
- they are not compatible with most ABS system because they doesn't lubricate the ABS pump like a glycol based fluid.
- putting this fluid in systems which have had DOT3/4 fluid in will cause the seals in the caliper and master cylinders to malfunction. Which means they need replacing. Which is expensive.
Oh, and don't ask me why DOT5.1 is glycol and DOT5 is silicon based. It doesn't make and sense to me either.
* There has been some discussion as to the use of DOT4 fluid in Toyotas that recommend DOT3 fluid - apparently something in the Toyota braking system doesn't play well with DOT4 fluid, particularly the master brake cylinder seals. The discussion about this can be found in the archives at the UK Pruis yahoo group.
Brake warning lights
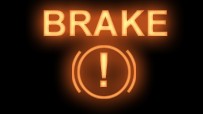
Most cars nowadays have a brake warning light on the dash. Its purpose is to alert the driver that something is wrong in the braking system somewhere. If it comes on, check the owner's manual to find out its meaning. Unlike the single-purpose ABS warning light, the brake warning light doesn't have a standard meaning; it could be used for multiple purposes. For example, the same light may be used to show that the hand brake (parking brake) is on. If that's the case and the car is being driven, the smell of burning brake dust ought to have been a clue though. The light can also indicate that the fluid in the master cylinder is low. Each manufacturer has a different use and standard for this light. Which is nice. Because it would be such a drag if the same indicator meant the same thing in every vehicle.
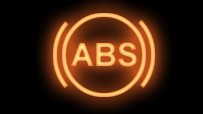
ABS-equipped car, typically also have a second light - the ABS light. If it comes on, get it seen to as soon as possible. It means the ABS computer has diagnosed that something is amiss in the system. It could be something as simple as dirt in one of the sensors, or something as costly as an entire ABS unit replacement. Either way, if that light is on, the ABS isn't working and the car is now endowed 1980's brakes. It's important to note that this light normally comes on when the ignition is first switches on, and then switches off a few seconds later. If it stays on, blinks, throbs, flashes or in any other way draws attention to itself, take note. It's not doing it just to please itself.
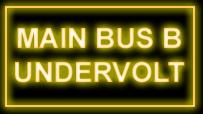
If you see this light on your dashboard, then congratulations - you're flying the service module on an Apollo mission. The bad news is that you've got a current drain somewhere and your main batteries are critically low. Either way, drop me a line and let me know how you snagged a seat on a spaceflight - I'm dying to know.
And finally....LED replacement bulbs
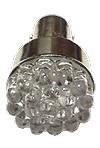
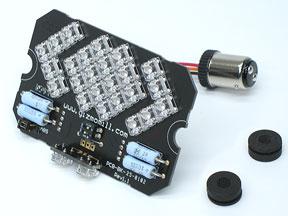
There are plenty of websites and automotive shops stocking LED replacement bulbs for cars and motorbikes. The most basic replacements look like those on the right - a cluster of 19 or 24 LEDS (light emitting diodes) in a housing with a regular push-fit or bayonet plug on the back. The idea is that if brighter lights are desired, the tail or turn lights can be replaced with these LED replacements. There is a gotcha though that the manufacturers often hide in the smallest of small print. A lot of vehicles (cars and motorbikes) have onboard diagnostics which include a light check. Some of these use resistance to figure out if a bulb has blown. LED clusters have a radically different resistance to a filament bulb and its possible that when the bulbs are replaced with LED versions, the car will continuously indicate that one or more bulbs is burned out. Getting one step more severe, with LED turn bulbs, the indicators could flash quicker or slower than expected (older indicator circuits use the natural resistance of the bulbs in conjunction with the relay to dictate the flash speed). The worst case scenario though is ABS; some motorbikes have very tightly regulated voltages in their ABS systems and taking the filament bulb out of the brake light to replace it with an LED bulb can cause ABS errors and theoretically, an ABS shutdown. Granted thats worst-case scenario, but it is a possibility.
The way around all these electrical load problems is to add resistance or ballast to the bulb replacement, and this is becoming more common now. Essentially, resistors are added in-line with the LEDs to provide the same sort of resistance to current flow that an incandescent bulb would, thus making the retrofit kits far more compatible with existing car or motorbike electrical systems. CycoActive make kits like this for motorbikes now. To the left is an example which shows the LED unit as a complete replacement for the tail unit on a bike, with a bayonet connector to fit into the old socket. The blue items are the ballast resistors designed to induce sufficient load in the electrical system for the diagnostics to register the unit as a regular lightbulb.
Picture credit: CycoActive